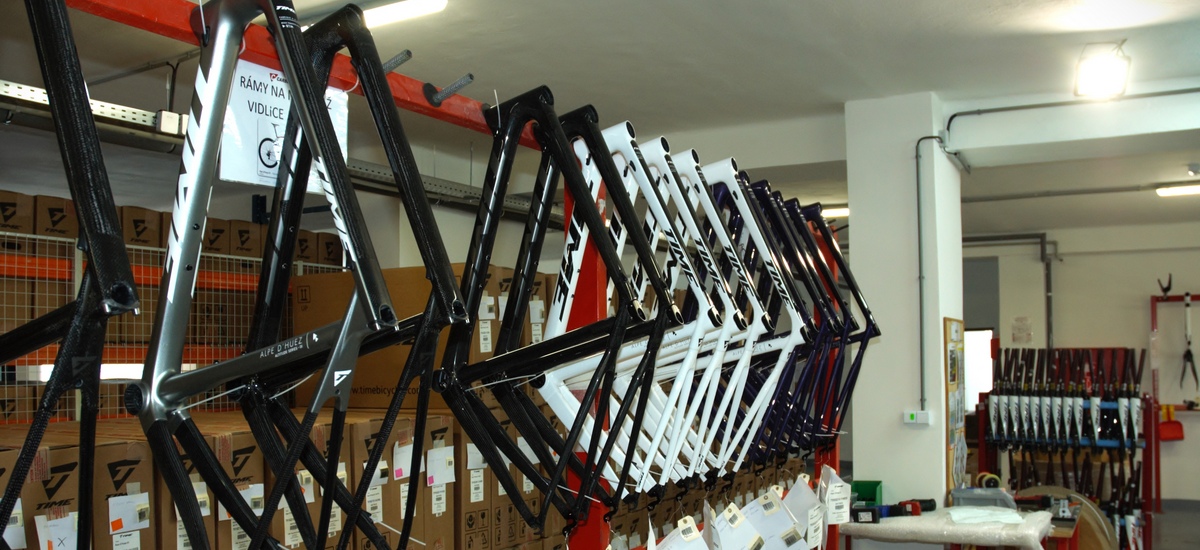
Karbon, kevlár vagy kompozit - Time Bicycles
Sikerült meglátogatnom egy rendkívüli gyárat, amely csúcskategóriás országúti vázakat gyárt, ezért egy olyan beszámolót hozok, amely elsősorban a dolgok technikai oldalára összpontosít.
Annak ellenére, hogy egy francia cégről van szó, nem kellett nagyon messzire utaznom. Valószínűleg sokak számára meglepő, hogy mindössze húsz percig tartott autópályán Pozsonyból észak felé haladva eljutni a gyártóüzem kapujáig. Aki még nem hallott róla, annak elárulom, hogy 2003 óta működik Gajaryban egy cég, amely karbon kerékpáralkatrészek gyártásával foglalkozik a Time Bicycles márka számára, és ha jól számolom, akkor ez közel 20 évet jelent.Egy kis történelem
Az 1980-as évek végén új anyag kezdi megrengetni a kerékpáros világot, így a TIME márka alapítója, Roland Cattin úr elindítja az első gyártósorokat. Miután maga köré gyűjtött néhány karbon technológia iránt elkötelezett rajongót, egyedi és valóban figyelemre méltó megoldásokat hozott a kerékpározás világába, amelyekről ebben a cikkben olvashatsz. A tulajdonos és alapító 2016-os sajnálatos halálát követően a francia óriás Rossignol vette át a céget három évre, de a prioritások átértékelése után, melynek során a Rossignol csak az MTB és e-MTB termékcsaládot tartotta meg a márka alatt, a Time Bicycles a jelenlegi tulajdonosok kezébe került. Hogy a cég alapítóját mennyire tartják nagyra, az azonnal kiderül az előcsarnokba lépve, ahol ez az emléktábla fogadja a látogatót.
Az előcsarnok második fotója koncentrált formában foglalja össze mindazt, ami ebben a szénszálas csodagyárban történik. Nagyon várom, hogy betekintést nyerjek a gyártócsarnokokba is, és valószínűleg hasonló örömöt érzek, mint a gyerekek csokoládégyár-látogatás közben .

Szénszálas termékek gyártása
Ez az a terület, ahol a precíz tervezés és az anyagválasztás lehetővé teszi egy olyan termék előállítását, amely a versenytársakkal szemben előnyt élvez.Ahogy a széntechnológiáról szóló korábbi cikksorozatban (linkek a cikk végén) említettük, a gyártásnak három alapvető szintje van. A legegyszerűbb és legkevésbé kifinomult a szövet kézi behelyezése és a gyanta beecsetelése a formába. Az esetleges vákuumozás és az autoklávban történő sütés valószínűleg ennek a folyamatnak a csúcsa. A második, tömegesen alkalmazott módszer az előre leszabott prepreg beillesztése (hogy felidézzük az emlékeket... ez egy részlegesen kikeményedett gyantával átitatott szövet) a formába, majd a forma kisütése a belső - üreges részek nyomás alá helyezését követően - ez történhet levegővel különböző légballonok vagy műanyag harisnyák segítségével.
Egyrészt tiszta és haladó technológia, de buktatói a belső nyomás alá helyezésben rejlenek. Senki sem tudja megjósolni, hogy mi történik a forma belsejében a sütés során, és hogy a nyomás egyenletesen oszlik-e el. Egy kis gyűrődés (a gyakorlatban általában néhány tucat gyűrődés) a műanyag légballonban elég ahhoz, hogy egyenetlenség vagy hiba jelenjen meg az anyagszerkezetben. Ezt az alapvető hibát kezeli az RTM - gyanta transzferformázás (resin transfer molding), amely során egy pontos meghatározott méretekkel rendelkező viaszmagot helyeznek a formába pontosan meghatározott számú szénszál-réteggel körülvéve. Miután a formát bezárták, a keletkező résbe nagy nyomás alatt gyantát préselnek, amely kitölti a teret, és nagyon precízen és szabályozott módon telíti vagy nedvesíti át a szálakat.
A szálakkal kezdődik
A Time Bicycles által alkalmazott RTM technológia egy lépéssel tovább megy. Úgy is mondhatnánk, hogy képesek karbonvázat kötni, vagy ha úgy tetszik, szó szerint "összefűzni" egy karbonvázat szénszálakból. Ezt az egyedülálló technológiát "Braided Carbon Structure" (BCS) névvel illették. Az anyagbemenet változó rugalmassági modulusú szénszálak jelentik, valamint más, szintetikusan előállított, Kevlar vagy Vectran kereskedelmi neveken ismert szálak.Ráadásul a fonás során különböző tuajdonságú szálakat is használnak (ezek tulajdonságait üzleti titok fedi), és ezeket az extra szálakat szénszálak kuszaságában csak a feketétől eltérő színük alapján lehet részben azonosítani. Ezeket a szálakat speciális gépeken fonják végtelen "csövekké", amelyeket méretre vágás után kézzel feszítenek viaszformákra.
A siker titka a szálak kombinációja, az ebből adódó tájolásuk és átfedésük a csatlakozási pontokon (ez a folyamat egyébként üzleti titok). Logikusan a kerékpárvázakban a legnagyobb terhelések olyan helyeken halmozódnak fel, mint a középtengely, a fejcső, a nyeregcső vagy a hátsó szerkezet. Ez az a pont, ahol a precíz tervezés és az anyagválasztás lehetővé teszi egy olyan termék előállítását, amely előnyben van a konkurenciával szemben. Az egyedileg meghatározott alapanyagok - "harisnyák" - fonása szinte korlátlan lehetőséget ad a tervezőnek, hogy minden részlet minden milliméterével eljátsszon, még a váz legveszélyeztetettebb helyén is. Az így elért szilárdság és merevség nagyon fontos, de nem az egyetlen fontos tulajdonság. A rezonancia csillapítása, a torziós merevség, valamint maga a váz tartóssága vagy ellenállóképessége a használat során szintén szerepet kap.
A szálak elhelyezése
A fent említettek szerint a teljes váz elkészítéséhez sokféle és különböző fonott harisnyát használnak, a sérülésnek kitett részeket pedig további kiegészítő szálakkal erősítik meg. Az egész folyamat természetesen szigorúan őrzött vállalati titok, és állítólag akár egy évig is eltarthat, amíg ezt a precíziós munkát az alkalmazottak megtanulják. Hogy mennyi időbe telt megtalálni a pontos eljárást, a szálak mennyiségét és irányát, a minél könnyebb és erősebb végtermék érdekében, azt a cég tulajdonosa nem árulta el nekem. Nem szabad elfelejteni, hogy a viaszmag és a fémforma közötti falvastagság változó, és így az is, hogy mennyi szenet és gyantát tudunk ebbe a résbe préselni." A képeken a váz végső szövetrétege látható száraz formában.Irány a forma
Miután a formába került, masszív prés segítségével lezárják, és megkezdődik az infúziós folyamat. A kevert gyanta nyomás alatt áramlik a formába az egyik oldalról, a felesleges levegő pedig a másik oldalról távozik. Mihelyt a buborékok már nem szöknek ki a formából, biztosak lehetünk benne, hogy a teljes tér egyenletesen és a forma utolsó sarkáig telítve van gyantával. A formát ezután pontos hőmérsékletre melegítik, hogy felgyorsítsák a kikeményedési folyamatot. A hőmérséklet azonban nem lehet túl magas, nehogy a formában lévő viaszmagok olvadni kezdjenek. Ezért a kikeményedés két fázisra oszlik. Az első a formában zajlik. Az eredmény egy szép, de meglehetősen nehéz váz, mivel az még fém tüskéket és csövek viaszmagjait tartalmazza.Ismét forróság
A vázat ezután "megszabadítják" a fémtől, és egy nagy kemencébe akasztják. Ott történik meg a gyanta végső kikeményedése, az úgynevezett "utólagos kikeményítés", és ezzel egy időben folyik ki a váz belsejéből az olvadt folyékony viasz. Ezt tartályokba gyűjtik, és visszakerül a gyártási folyamat elejére, ahol ismét magokat készítenek belőle a formához. A váz, ezúttal szinte végleges súlyában, számos szépítő eljáráson megy keresztül. Durva csiszolás, csiszolás és finomcsiszolás.Vázragasztás
A következő gyártási folyamat során a nyers váz (első rész) és a hátsó merevítők abba a terembe kerülnek, ahol ezeket az alkatrészeket összeillesztik, hogy egyetlen egységet alkossanak. Itt születik meg a végtermék általános geometriája és lényegében a végtermék szilárdsága. Minden váztípusnak és méretnek megvan a maga sablonja, az úgynevezett "gabarit", amelybe a vázat és a hátsó merevítőelemeket százmilliméteres pontossággal rögzítik.A Time Bicycles semmilyen módon nem takarja el ezeket az illesztéseket, és a végterméken is jól láthatóak az elválasztó síkok.

Végső módosítások
A következő helyiségben az összes szükséges furat kifúrása és marása következik, majd festés, matricázás és újabb lakkozás. A következő színkombinációk érhetők el: fehér, kék, piros, szürke vagy egy áttetsző lakkozás, amely kihangsúlyozza a karbontextúrát.A vázkészlet felületkezelés nélkül is megrendelhető, és otthon befejezhető saját ötlet és terv szerint. Ha pedig a gyári grafikát szeretnéd (ami egyébként nagyon szép), akkor a végső fényesítés és egy igazán precíz ellenőrzés következik.

Bilincsek és villavégződések
Ezek az apró részletek egy kerékpárvázon általában alumíniumból CNC technológiával készülnek. Nem így a Time Bicycles-nél (mivel tisztában vannak vele, hogy a dural-karbon illesztések általában problémásak), ahol hiába keresnéd a dural villavégződéseket. A tervezők itt is megtalálták a megoldást, és a CMT (Carbon Matrix Technology) nevű eljárással maguk állítják elő ezt a nagyon fontos alkatrészt. Az alapot egy külső beszállítótól származó aprított szálak és gyanta speciális keveréke adja, amelyet vastag lemezek formájában, fagyasztva szállítanak.Ezeket pontosan téglalap alakúra vágják és lemérik. Kíméletes felmelegítés után henger alakúra sodorják, majd pontos mérlegelés után ismét lefagyasztják őket. A préselési folyamat a dugattyúrúdba való behelyezésével kezdődik, és több mint 100 tonnás erővel nyomják be az előmelegített formába. Miután "befecskendezték", megkezdődik a sütés folyamata. A nagy nyomás és a pontos hőmérséklet biztosítja, hogy a formában lévő összes rést kitöltsék, és az eredmény egy rendkívül erős, funkcionális, könnyű és gyönyörű alkatrész lesz.

Villa
A villák külön fejezetet érdemelnek. A gyártási technológia által adott magas minőség és a figyelemre méltó merevség mellett a cég még tovább ment. A passzív rezgéscsillapításon túl, amelyet a különböző szintetikus szálak megfelelő kombinációjával "szőttek" a konstrukcióba, részben képes kiküszöbölni a 25 és 50 Hz közötti rezonanciákat, amelyeket a durva aszfalton való tekerés generál.Ez egy pontosan kiszámított rezonáns lemezre, vagy nyelvre beágyazott súly elvén működik. Egy felnifékes villán két ilyen súly van (egy-egy lábon). Egy tárcsafékhez tervezett villában egy nagyobb súly található azon a részen, ahol a fék nincs rögzítve. Ez a rendszer nagyon könnyen felismerhető a villa megnagyobbításáról ott, ahol ez a súly el van rejtve. Az ilyen villa a vázhoz extra tartozékként rendelhető.
Gyártási perspektíva
A négy nagy gyártócsrnok bejárása nem hagyott kétséget afelől, hogy nincs gond az eladásokkal, sőt fél évre előre elkelt minden. A meghatározó piac az Egyesült Államok és az európai országok közül (természetesen történelmi okokból) Franciaország. Főleg vázszettekre koncentrálnak, mivel a legtöbb vásárló inkább saját maga választja ki az alkatrészeket.Jó hír a munkakeresők számára, hogy a cég egy új fejlesztési részleg létrehozását tervezi a cég gajarói telephelyén. Ezért, ha úgy érzed, hogy alkalmas lennél karbon termékek tervezésére, értesz a 3D grafikai programokhoz, jól beszélsz angolul (esetleg ha franciául, az még jobb...) és nem vagy messze Gajarytól, próbáld meg felvenni a kapcsolatot a HR osztállyal, mert az "álommunka" lehet hogy épp rád vár... .